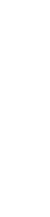
Manufacturing Process
During the manufacturing stage, the kitchen goes through several stations and stages that are determined based on several factors and standards specific to the company. The beginning of the kitchen manufacturing stages is the arrival of the detailed kitchen manufacturing plan to the factory system with the customer’s number and information that will accompany the kitchen in all stages of manufacturing and post-manufacturing.
Raw Materials
After receiving the plan, the process of collecting raw materials for the kitchen begins from the company's stores and suppliers approved by the company.
MANUFACTURING
When the raw materials are completed, the kitchen enters the manufacturing area in order after the kitchens that preceded it in the role, and in the manufacturing process, cutting, assembling, and painting (if necessary) the basic body of the kitchen until it is assembled in the form of units of various sizes, after which all the basics, luxuries and additions for the kitchen are assembled on The hand of the most skilled craftsmen until a complete kitchen is formed in the assembly area, and the units are transferred to the factory inspection area.
QUALITY INSPECTION
Upon completion of the assembly of the kitchen and the arrival of the final product ready without shortage or problems, the kitchen enters the final manufacturing inspection area for quality, where each unit in the kitchen is examined separately, with great accuracy and high craftsmanship.
PACKAGING
Upon approval, the kitchen is sterilized and cleaned from the inside and outside with special materials suitable for the product, and it is wrapped All units are placed, and a sticker containing the customer’s information and details is placed, as well as a sticker containing the person who examined the unit and approved its removal outside the factory.
TRANSFER TO WAREHOUSE
Upon completion of manufacturing and packaging, the units are transferred to the company's stores, where the kitchen is distributed in its correct place inside the stores, and during that period, communication is made with the customer to appropriately and determine the date of delivery of the product to his home.
DELIVERY TO CUSTOMER
When the delivery time comes, the kitchen is delivered to the customer's home through the company's delivery crew, with transportation equipment suitable for the location of the house and the surrounding environment.
CABINET INSTALLATION
Within a few hours, the team of the assembly and installation unit communicates with the customer to arrange a date to install the kitchen in the customer's house in a way that satisfies him completely.
COUNTERTOP INSTALLATION
Upon completion of the kitchen (wood) installation stage, measurements are taken by the company’s staff specialized in marble (blind) and sent to the company’s marble factories. Within a few days, the marble (blind) has been installed in the customer’s house with all the elements of the customer’s dream kitchen completed and the kitchen delivered. To the customer, making sure that he is completely satisfied with the project.
Raw Materials
After receiving the plan, the process of collecting raw materials for the kitchen begins from the company's stores and suppliers approved by the company.
MANUFACTURING
When the raw materials are completed, the kitchen enters the manufacturing area in order after the kitchens that preceded it in the role, and in the manufacturing process, cutting, assembling, and painting (if necessary) the basic body of the kitchen until it is assembled in the form of units of various sizes, after which all the basics, luxuries and additions for the kitchen are assembled on The hand of the most skilled craftsmen until a complete kitchen is formed in the assembly area, and the units are transferred to the factory inspection area.
QUALITY INSPECTION
Upon completion of the assembly of the kitchen and the arrival of the final product ready without shortage or problems, the kitchen enters the final manufacturing inspection area for quality, where each unit in the kitchen is examined separately, with great accuracy and high craftsmanship.
PACKAGING
Upon approval, the kitchen is sterilized and cleaned from the inside and outside with special materials suitable for the product, and it is wrapped All units are placed, and a sticker containing the customer’s information and details is placed, as well as a sticker containing the person who examined the unit and approved its removal outside the factory.
TRANSFER TO WAREHOUSE
Upon completion of manufacturing and packaging, the units are transferred to the company's stores, where the kitchen is distributed in its correct place inside the stores, and during that period, communication is made with the customer to appropriately and determine the date of delivery of the product to his home.
DELIVERY TO CUSTOMER
When the delivery time comes, the kitchen is delivered to the customer's home through the company's delivery crew, with transportation equipment suitable for the location of the house and the surrounding environment.
CABINET INSTALLATION
Within a few hours, the team of the assembly and installation unit communicates with the customer to arrange a date to install the kitchen in the customer's house in a way that satisfies him completely.
COUNTERTOP INSTALLATION
Upon completion of the kitchen (wood) installation stage, measurements are taken by the company’s staff specialized in marble (blind) and sent to the company’s marble factories. Within a few days, the marble (blind) has been installed in the customer’s house with all the elements of the customer’s dream kitchen completed and the kitchen delivered. To the customer, making sure that he is completely satisfied with the project.